1. Correctly install the rubber roller bearings: first clean both sides of the rubber roller, and then select bearings whose specifications and models meet the design requirements of the machine, and apply a uniform layer of lubricating oil on each mating surface, and then use the bearing installation The special sleeve exerts even force on the bearing to make it smoothly installed in place. Never apply force directly to the bearing surface to avoid damage to the bearing.
2. Regulate the pressure between the ink rollers: In the printing process, the ink rollers and ink rollers must continuously and evenly provide the appropriate amount of water and ink to the printing plate, so as to obtain printed products with consistent ink color. Therefore, proper pressure must be maintained between the rubber roller and the rubber roller, and between the rubber roller and the printing plate, in order to achieve good ink transfer. In order to ensure the pressure between the water roller and the ink roller, the rubber roller must adopt the method of roller width, which mainly includes the following points. (1) Add appropriate amount of yellow ink evenly on the clean rubber roller, and then run the machine to make the ink evenly distributed on the surface of the ink roller. (2) Jog the printing machine to check the width of the pressure bar. It is worth noting that before checking the width of the pressure bar, the printing machine should be kept stationary for about 20 seconds, and then the printing press can be moved to get a clear pressure bar again. (3) Priority should be given to adjusting the pressure between the inking roller and the inking roller, and then adjusting the contact pressure between the inking roller and the printing plate, and then adjusting the pressure between the other inking rollers respectively.
3. Correctly disassemble the rubber roller: each time the rubber roller is disassembled, the employees should coordinate and unify the adjustment screw to loosen 2 turns. When reinstalling the rubber roller, only need to tighten 2 turns in the opposite direction. Even if there is an error, it can be fixed quickly. At the same time, check the quality of each bearing. If it feels swaying, blocking, etc., it must be replaced immediately.
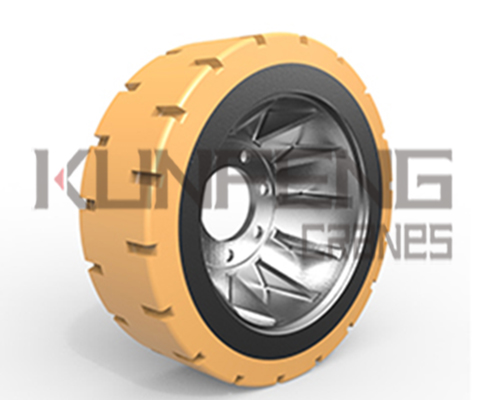